The Best Brine Tanks
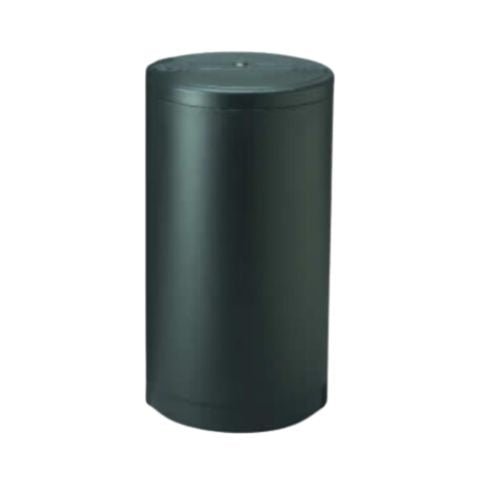
Overview of Structural Commercial Brine Tanks
Structural commercial brine tanks are essential components in many industrial processes, serving as storage solutions for brine solutions used in various applications. These tanks are designed to handle the corrosive nature of brine, ensuring long-term durability and operational efficiency. Brine tanks play a crucial role in industries such as water treatment, food processing, pharmaceuticals, and chemical manufacturing. Their ability to store and dispense large quantities of brine makes them indispensable for processes that require consistent and reliable brine solutions.
This article aims to provide a comprehensive overview of structural commercial brine tanks, including their design, materials, applications, and maintenance. By the end of this guide, readers will have a thorough understanding of how these tanks function and their significance in various industrial contexts.
Structural commercial brine tanks are specialized containers designed to store and manage brine solutions. Brine, typically a high-concentration solution of salt (sodium chloride) in water, is used in numerous industrial processes, including water softening, de-icing, and food preservation.
Key features of structural commercial brine tanks include robust construction materials, corrosion-resistant coatings, and various safety and monitoring systems. The development of brine tanks has evolved significantly over the years. Early brine storage solutions were rudimentary and often made from materials that quickly corroded. Advances in materials science and engineering have led to the development of more durable and efficient tanks.
Key features of structural commercial brine tanks include robust construction materials, corrosion-resistant coatings, and various safety and monitoring systems. The development of brine tanks has evolved significantly over the years. Early brine storage solutions were rudimentary and often made from materials that quickly corroded. Advances in materials science and engineering have led to the development of more durable and efficient tanks.
Key milestones include the introduction of fiberglass-reinforced plastic (FRP) in the 1960s, which offered superior corrosion resistance, and the development of high-density polyethylene (HDPE) tanks in the 1980s, which combined durability with cost-effectiveness. Recent innovations include smart monitoring systems that enhance operational efficiency.
Vertical brine tanks are commonly used in applications where space is limited. They are designed to maximize storage capacity while minimizing the footprint. Horizontal brine tanks are preferred in situations where height restrictions are a
concern. These tanks offer easy access for maintenance and cleaning.
concern. These tanks offer easy access for maintenance and cleaning.
Custom-designed tanks cater to specific industrial needs, including unique shapes, sizes, and features tailored to particular applications. HDPE is a popular material due to its high resistance to chemicals and corrosion, lightweight nature, and ease of fabrication.
FRP tanks offer excellent corrosion resistance and durability. They are often used in highly corrosive environments and can be customized for additional strength. Steel tanks, particularly those made from stainless steel, provide superior strength and durability. They are ideal for high-pressure applications and environments where temperature control is crucial.
Ensuring the structural integrity of brine tanks is paramount. This involves using materials and construction techniques that withstand the corrosive nature of brine and the pressures exerted by large volumes of liquid. Corrosion resistance is a critical factor in the design of brine tanks. Materials like HDPE and FRP are chosen for their ability to resist chemical degradation, extending the lifespan of the tank.
Proper sizing is essential to meet the specific needs of an application. Factors to consider include the volume of brine required, the available space, and the operational demands. Safety features such as overflow protection, pressure relief valves, and secure lids are integral to prevent accidents and ensure safe operation.
In water treatment plants, brine tanks are used for regenerating ion exchange resins in water softeners. They ensure a consistent supply of brine solution, which is essential for effective water softening. Brine is used extensively in the food and beverage industry for processes like pickling, curing, and de-icing. Brine tanks in this sector must meet strict hygiene and safety standards. The pharmaceutical industry uses brine for various purposes, including as a solvent in drug manufacturing and for sanitation purposes. Tanks used in this industry must comply with stringent regulatory standards. In chemical manufacturing, brine tanks store raw materials and intermediates. The corrosive nature of many chemicals necessitates the use of tanks made from highly durable materials like FRP or stainless steel. Brine solutions are used in agriculture for tasks such as fertilizer preparation and irrigation. Tanks in this industry need to be robust and resistant to both chemical and physical damage.
Proper site preparation is critical for the successful installation of brine tanks. This includes ensuring a stable and level foundation, adequate drainage, and accessibility for maintenance. The foundation must be capable of supporting the weight of the filled tank without settling or shifting. Concrete pads are commonly used for this purpose.
Structural commercial brine tanks are essential for various industrial applications, offering durability, efficiency, and cost-effectiveness. Proper selection, installation, and maintenance are crucial for maximizing their benefits.
Investing in high-quality brine tanks can significantly enhance operational efficiency and reduce long-term costs. Organizations should carefully consider their specific needs and choose the appropriate tank design and material.